The energy consumption of the mixer-settler is mainly affected by the following factors:
Processing capacity: The larger the volume of liquid handled by the mixer-settler, the higher the energy consumption required. Increased throughput may require higher mixing speeds or longer runs, thereby increasing energy consumption.
Properties of the liquid being processed: The viscosity, density, concentration and particle size distribution of solid particles and other properties of the liquid will affect the energy consumption of the mixer-settler. For example, highly viscous liquids or liquids with a high concentration of solid particles require more energy to mix and settle.
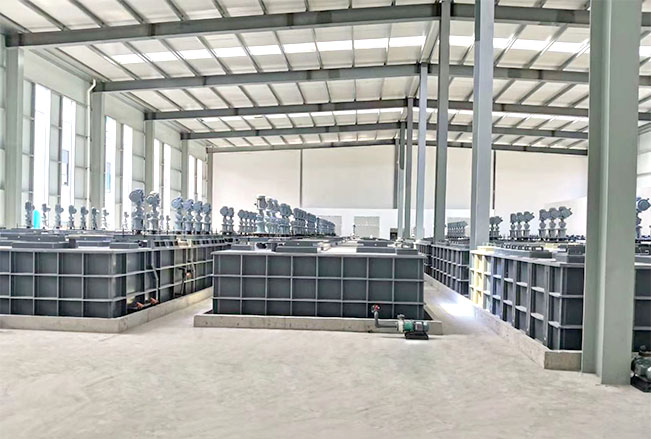
Stirring method and intensity: The stirring method and intensity in the
mixer-settler directly affect energy consumption. Although too strong agitation can improve the mixing effect, it will also increase energy consumption; while insufficient agitation may lead to uneven mixing and affect the settling effect.
Equipment design and manufacturing quality: Factors such as the equipment’s structural design, material selection, and manufacturing accuracy will all affect its energy consumption performance. The optimized design of the mixer-settler can reduce fluid resistance and improve energy utilization efficiency.
Control of operating parameters: The operating parameters of the mixer-settler, such as liquid inlet flow rate, stirring speed, operating time, etc., need to be reasonably adjusted according to the actual situation. Unreasonable operating parameters may lead to increased energy consumption or poor processing results.
Environmental conditions: Environmental temperature, humidity and other factors may also have a certain impact on the energy consumption of the mixer-settler. For example, a high-temperature environment may cause poor heat dissipation of the device and increase energy consumption.